Great opportunities within the Dispal® business
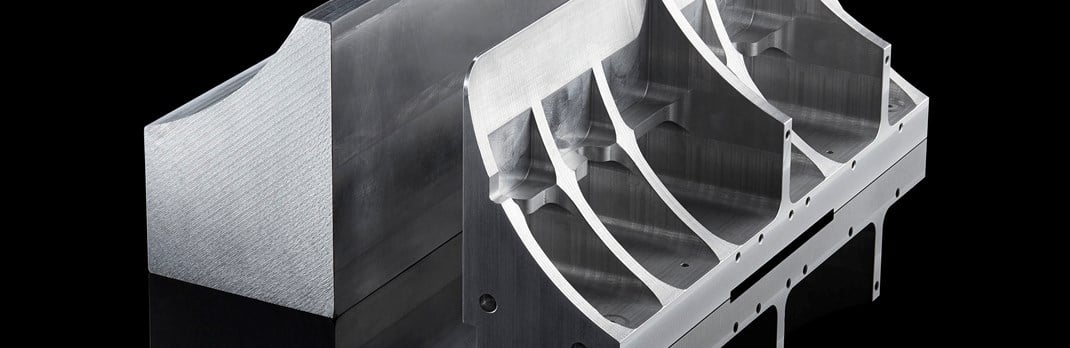
Gränges Powder Metallurgy (GPM) has the objective to become leading aluminium powder producer globally. With atomization capabilities in St Avold, France and Velbert, Germany, GPM has the powder production capacity of 2,500 tonnes per year. We talked to Joakim Andersson, Sales Manager at GPM about the opportunities he sees within the Dispal® business.
Within GPM one of the products are Dispal®. This product has a high performance and strong material properties combined with low weight. The Dispal® is spray-compacted Al material containing a high amount of Si (from 17 % up to 35 %), which gives unique material properties. Dispal® can be used for various applications in different industries. Examples range from linear technology over oil pump gears to bearing caps and more sophisticated industry products such as aerospace and industrial robots. Other areas are for instance automotive, optics and electronics.
The Dispal® business today, is primarily concentrated in Europe (DACH region), but there are great opportunities within other markets going forward.
There are great opportunities worldwide. In America for example, there is a lot of high-tech companies in the semiconductor manufacturing and Aerospace industry. The Asian market is driven by innovative countries like South Korea and Japan with big “pick and place” manufacturing companies, Joakim says.
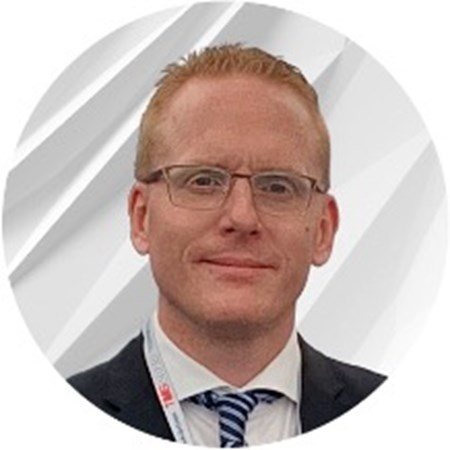
What are Gränges’ advantage regarding the Dispal® product compared to our competitors?
Most of our sales right now is towards PCB, semiconductor machine manufactures, Joakim says.
Joakim, can you go through some of the Dispal® advantages?
The low weight – These machines have an extreme high operating frequency, meaning 10–15 operation/sec, which means high acceleration and braking. Our DISPAL® product has a very low weight compared to competing materials like Titanium alloys which means low interia – low energy consumption.
The thermal expansion – Due to the high Si, 17–35 %, the material has a very low thermal expansion which has a similar level as steel or titanium. This is very positive due it is a lot of dissipated heat from the linear motors operating in the pick and place machine. Another part is that the CTE (thermal expansion) is low and the accuracy/precision will be higher in the machine.
Its stiffness – Due to the demand of high precision in the machine, the stiffness (less flexing) of the material is very important. The stiffness is in the same level as titanium alloys and roughly 25–30 % higher than conventional aluminium alloys.
The machinability – Due to the process characteristics, the cooling rate during solidification is much higher and this creates an extreme fine and homogenous structure which itself will create a more smother and predicted machinability.
And finally, the cost – Compared to similar alloy systems with the same properties as titanium alloys, the cost is considerably lower.
What do you think is/are the biggest opportunities/challenges with Dispal®?
The biggest opportunities right now are in the semiconductor machine manufacturing driven by the 5G development. We can also see opportunities in the optical and satellite industries. Due that this material has a good fit in combustion engine, for example in inlet valves and cylinders it will be a challenge to find similar applications in the electrical vehicle segment, Joakim concludes.