Happy Housekeeping
Like many companies, Gränges has been inspired by the Toyota Production System. Here’s a look at the guiding principles of the company’s lean approach to manufacturing, and how employees are adding value to the organization.
Boosting productivity through the use of lean, effective working methods has long been the goal at Gränges, and since the implementation of the Gränges Production System (GPS) at all production facilities in the summer of 2017, activities have been in full swing.
Paul Neutjens, Senior Vice President Process Engineering and Operational Development, says: “It’s when we all embrace the concept of GPS and take responsibility for implementing its principles that we achieve lasting results. The secret to success is good leadership. It’s remarkable to see how engaged our staff are in creating order in the workplace. People are central to making this system work.”
In fact, the engagement of people is one of the overarching lean manufacturing principles covered by GPS, the others being:
• the elimination of waste
• making what the customer wants when they want it
• operating as efficiently as possible at the lowest possible cost
• maintaining reliable processes and equipment
• environment, health and safety
• housekeeping and cleanliness
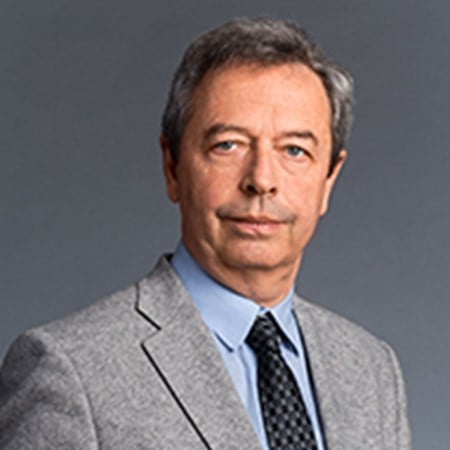
The structured "5S" method (see box below) is an effective tool used for applying the principles of GPS. Gränges teams all over the world are discovering that 5S pays off - that by maintaining an organized workplace they can raise quality, lower costs, decrease lead time and boost productivity and saftey.
Depending on the individual's role and responsibilities, they might reorder storage facilities, clear passageways, label shelves and drawers, put up sign posts in restricted areas, replace worn-out tools or demarcate work zones. Anything goes when it comes to organizing the workplace in a way that allows problems to be detected easily.
“So far, we’ve divided up our production facilities, starting with pilot projects in certain areas, and we are expanding our efforts to cover entire plants, worldwide,” says Neutjens.
In Shanghai, for example, the plant has been split into about 70 areas. Employee teams are implementing 5S in nine pilot areas where they are establishing the foundations for a continuously improving operation. Now they just need to keep up the good work. Because good housekeeping in the workplace is a bit like at home: no matter how satisfied you are with the order you create, unless you maintain it, things quickly slide back into a state of chaos.
“If you don’t keep equipment surfaces clean, it’s hard to spot a problem and take action,” says Neutjens. “Imagine if a stack of boxes is misplaced on the shop floor, causing a blind spot... A forklift truck might come around the corner and hit someone."
"GPS is a journey, and it takes time. In fact, it takes forever since you can always improve things. With time, things just get better and better."
Gränges 5S: the secret to an organized workplace
• Sort. Go through your workplace, removing any unnecessary materials and keeping only the necessary items.
• Set in order. Arrange your workplace in a logical manner, so the layout enables a good workflow, using labels, markings and color coding to create visual order and ensuring that any tools and documents used daily are readily accessible and stored in the order of use.
• Shine. Do a thorough spring clean of your workplace, keep it tidy and take photos of the results.
• Standardize. Agree on and establish standardized routines.
• Sustain. Maintain what you have achieved in S-steps 1–3, using checklists to ensure that agreed standards are met.