The stars of the cold rolling mill
A team at Gränges in Finspång managed to decrease the coil changing time at one of the cold rolling mills by 25 percent, while increasing the average machine speed by 35 percent. All without any investments. Their tools: clear goals, a consistent GPS focus and lots of cooperation and commitment.
In 2016, as Gränges in Finspång planned to ramp up its production, a bottleneck was identified: the cold rolling mill 2751. This machine is one of the most critical for the whole production at the facility; all material has to pass through it in the production chain, being the first cold rolling mill after the hot rolling.
Bottleneck problems at mill 2751 would mean that the production volumes the facility was aiming for couldn’t be met. So the stakes were high when the task was handed to production leader Magnus Jonsson.
“We had a systematic approach right from the start, I think that’s one of the reasons why we managed to reach such good results,” he says.
This systematic approach included gathering all the shift personnel at the mill, Attila Szöcs from maintenance and Lasse Svensson from technical support, for initial meetings where everyone could contribute with ideas on how to meet the goals. In keeping with the company’s GPS method, a document, an “A3”, was created. Other GPS tools, such as 5S, SMED and daily meetings were also used.
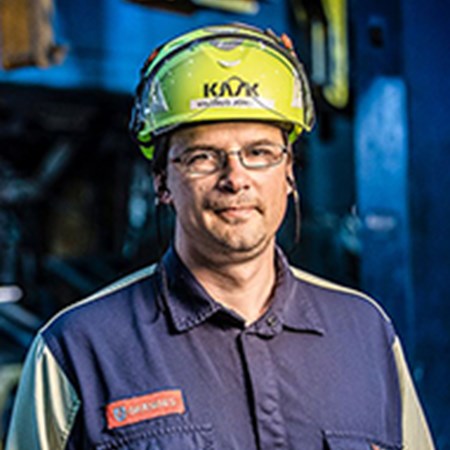
“In the A3 we worked a lot with breaking down the overall goals into concrete targets and what they mean for us, on our particular machine. After that, the A3 has been our steering document, with clear and relevant key performance indicators, KPI’s.” he says.
After initial meetings where everyone involved got onboard and “gave their OK”, Magnus Jonsson says that everything has gone smoothly. In a year, they’ve seen the coil changing time reduced by 30 seconds, and the average machine speed increase from 320 to 355 meters per minute.
The results have been recognized with the team being rewarded the 2019 Gränges Company Awards, in the Continuous Improvement category.
“I think we managed to bring out an element of performance in everybody, and a competitive instinct,” he says.
Good cooperation between the shift personnel and the supporting functions from maintenance and technical support, have been crucial to the team’s achievement, Jonsson emphasizes. He is especially proud of the fact that all of the improvements have been made without any additional investments.
What are your best tips to others in the Gränges organization working with improvement projects?
“Create very clear goals, KPI’s – that’s really important for motivation. And make sure you cooperate closely – get out on the shop floor and discuss the goals and how you plan to fulfill them.”
The jury’s motivation in summary
“Gränges Finspång has managed to structurally remove bottlenecks at the TCM. They have done so driving a performanceoriented culture whereby the mill speed and coil changeover is continuously monitored by the operators. The GPS tools such as 5S, SMED and Daily management are used to lock-in the achievements. This is a true example of Continuous Improvement that started two years ago and continued to deliver results.”
Team members: Operators, the support team around 2751 (maintenance and technicians) and Magnus Jonsson.