Energy savings – not a Scrappy project
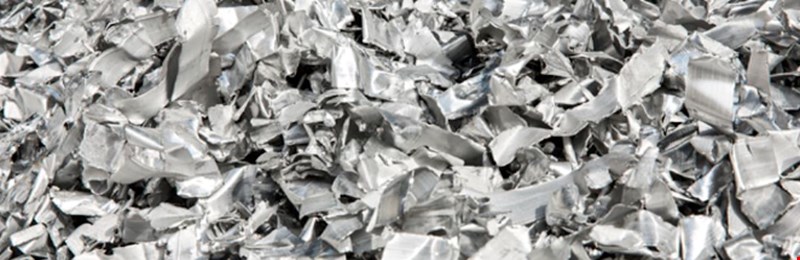
To have good and sustainable solutions for energy consumption is very important for any manufacturing company. We talked to Paul Neutjens, Gränges’ SVP Process Engineering & Operational Development and the driver of Gränges’ Energy Savings Project.
What is the Energy Savings Project about?
The energy savings project has to do with recycling scrap, and it is part of Gränges’ overall sustainability targets. In the framework of our GPS work we have an objective to address critical processes. We look at our casting and melting processes where one of the main topics is energy savings. On the Group level, all our cast houses spend 560 gWh (Gigawatt-hour) together per year on gas, fuel and electricity and this is about half of our total energy spent within Gränges. If you compare that with an average household which consumes about 25 mWh per year we consume the equivalent of about 20 000 households.
On Group level one of our sustainability targets is to reduce the energy intensity by 17 % in 2025, comparing to the 2017 levels.
Paul Neutjens, is the driver of the Energy Saving Project.
How have you start working with this project?
Within the framework of GPS (Gränges Production System) we work closely together with the operators on the factory floor. What is very important when we re-melt scrap and ingots is how we load the furnaces and how the sequence of the different steps is done. It all started with a pilot project in Shanghai on casting center #3 where we look at the sequence of all those operations in a cycle. The cycle is going from casting one drop of slabs to the next drop of slabs. Within this cycle the loading and melting of the ingots, the alloying elements and the various types of scrap is very important as it has a big impact on the energy needed.
In order to optimize this process, we consider three major elements. These are:
1) The human element: How the operators follow a certain sequence in the melting process.
2) The technology element: The type of burners, sensors and other hardware and how we monitor the different parameters.
3) The artificial intelligence element (AI): We will start to use AI to optimize the parameters and give suggestions to the operators and the engineers on how to run the process.
The first element is human based. It consists of the loading practice of the metal. For example, the type of scrap is important, which scrap you load first, the light scrap or the heavy scrap and how many times you open the doors. After that you have the heating, which is done by the burners, and finally the cleaning or as it is sometimes called; “drossing”. During this process you need to clean the melt, this is often a semi-manual activity as you must open the door and work with big scrapers to clean the melt. It is a collaboration together with the operators in the daily management and allows us to follow the specific sequence in detail and to see how we can optimize this in a better way.
The second element is based on technology, where the parameters of the process are measured and used to steer the process. As examples Paul mentions the parameters of the burners where we look at the oxygen to fuel ratio, the pressure and the temperature of the roof of the furnace. We have a lot of sensors in that process that measure the various parameters and we are investigating how we can better use these parameters to improve the process.
The third element is artificial intelligence (AI) and specifically, so called “machine learning” which will be used to continuously analyze all parameters. Machine learning will basically be a specific algorithm that takes all those input parameters to self-teach the algorithm in order to make suggestions to support the operation and thereby improve certain output parameters.
How many people are part of the project team?
A team in Shanghai started the pilot project on casting centre #3 last year. Since the beginning of this year we started to benchmark the parameters also with furnaces in the other operations, in Finspång (melting furnace 144) and in Huntingdon (melting station 805). Niclas Gustafsson, at R&I in Finspång, is leading the benchmark team, and Marcus Walberg is responsible to provide the AI expertise. The intent is to integrate the project in the operations via the GPS teams across Gränges.
If we look at Finspång we have a separate project that is a proof of concept for the machine learning. It is connected to the overall energy saving project, and is led by Johan Kirsch, an engineer in the cast house. There a few people working with this and the steering committee consists of myself, Patrik Sivesson and Kent Schölin. Marcus Wallberg is also involved in the project regarding primarily the AI part.
What do you hope this project will bring. What are your targets?
We are finetuning the targets as we speak, but I hope that at the end of the day we can save 10% of our energy consumption. It is not just energy savings. The project will hopefully also result in less waste in terms of dross generation, better scrap utilization, lower maintenance cost and shorter melting cycle times. The main objective is energy savings, but we are confident that we will get spin-off effects in other parts of the operations such as cost reduction as well as a reduction of the environmental footprint. The more energy you save the more CO2 emissions you reduce.